Thermal power engineering
We are one of the world's leading players in automation in the field of conventional energy. Our control systems and know-how ensure the operation of thermal power plants in 55 countries around the world.
We offer a wide portfolio of products within the 60-year history of deliveries to thermal energy. We implement small to medium-sized orders in which we deploy our own SandRA control system. We provide customers with their long-term and reliable operation, including warranty and post-warranty service.
Control and management systems
Comprehensive design and type solutions for operated and newly built power plants, heating plants and incinerators from design to service
Our own development
Our own platform SandRA for meeting customer requirements for various types of operated technologies
Tradition and stability
Control of thermal power plants and heating plants since 1972 and operation of 250 power blocks
in more than 55 countries around the world
Power plants
Thermal energy is a segment engaged in the production of energy (electric, thermal) by burning fossil fuels, biomass or waste, where customers require the ecological operation of production technology with maximum efficiency. The technology is designed for stable and long-term operation without frequent shutdowns.
We offer partial and comprehensive solutions for the management of technological operating sets for the control of boilers, engine rooms and auxiliary non-block operations.
We provide detailed design of solutions according to customer requirements. We process projects from solution design, through production, testing, assembly to commissioning. We also offer the preparation of production documentation.
Advantages of our supplies
- Our own platform SandRA Synergy with a long life cycle
- Openness of the control system
- Use of IoT technology for remote access and operation diagnostics
- Our own development and adaptation to technology requirements
- Gradual replacement or migration of control systems throughout the life cycle
- Optimization of operation and reduction of operating costs
- Interconnection of information systems (unified repository for data sharing and management)
- Ability to ensure compliance with cyber security requirements
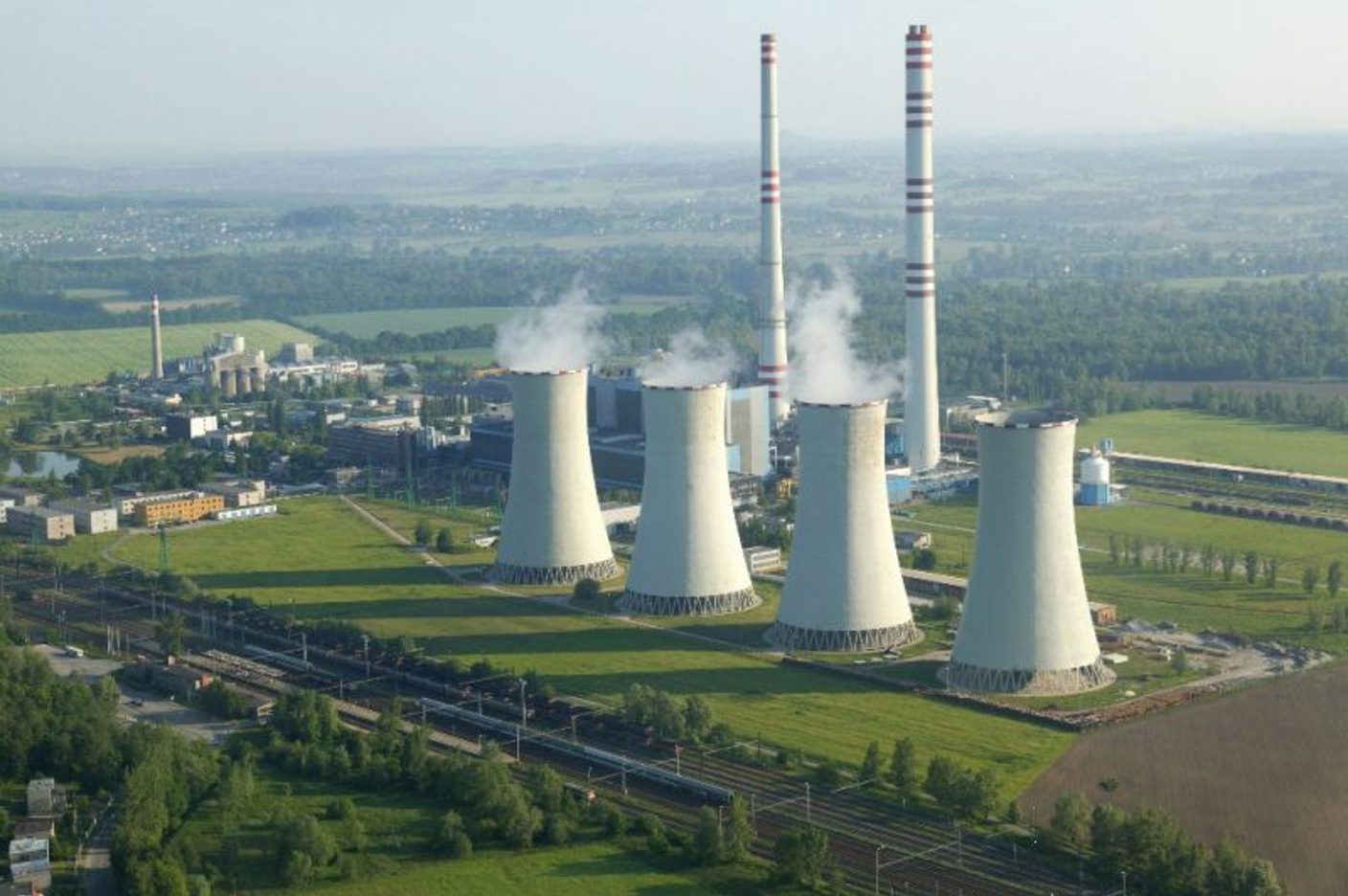
Heating plants
We supply control and management systems to operated and new heating plants in the Czech Republic and abroad. We develop, design and manufacture control systems for various types of boilers and for the control of entire technological blocks. We focus on the control of so-called block and non-block operating files. We supply control technologies to reduce emissions of sulfur, nitrogen, mercury and dust particles.
We provide design and supply of control systems for heating plants using any combustion technology. We offer customers comprehensive services in the modernization of control and management systems. In all activities, we adhere to strict operating conditions, including cyber security.
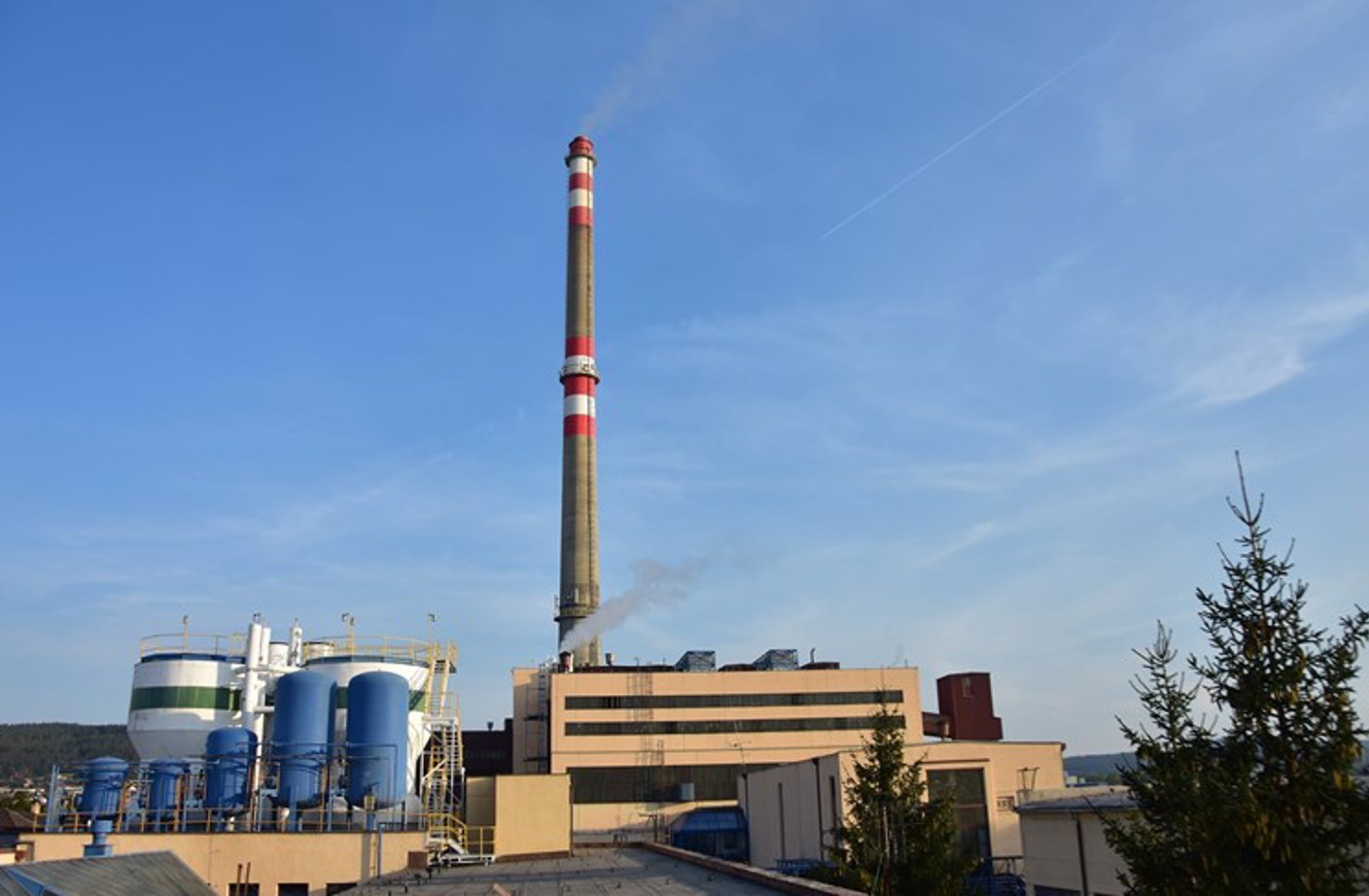
Advantages of our supplies
- Our own platform SandRA Synergy with a long life cycle
- Openness of the control system
- Use of IoT technology for remote access and operation diagnostics
- Own development and adaptation to technology requirements
- Gradual replacement or migration of control systems throughout the life cycle
- Optimization of operation and reduction of operating costs
- Interconnection of information systems (unified repository for data sharing and management)
- Ability to ensure compliance with cyber security requirements
Incinerators
We implement control and management systems for operated and new waste incinerators in the Czech Republic and abroad. We develop, design and manufacture control systems for various types of boilers and for the control of entire technological blocks using waste incineration energy of various types. We have references in large incinerators, at the same time we are able to supply complete I&C and electrical parts for small local incinerators. We focus on the management of so-called block and non-block operating files. We manage technologies to reduce emissions of sulfur, nitrogen, mercury and dust particles.
Advantages of our supplies
- Ability to use IoT for remote access and operation diagnostics
- Comprehensive supplies, including analysis and optimization of operation
- Openness of the control system
- Possibility of interconnection of information systems (unified repository for data sharing and their management)
We provide design and supply of control systems for heating plants using any combustion technology. We offer customers comprehensive services in the modernization of control and management systems. In all activities, we adhere to strict operating conditions, including cyber security.
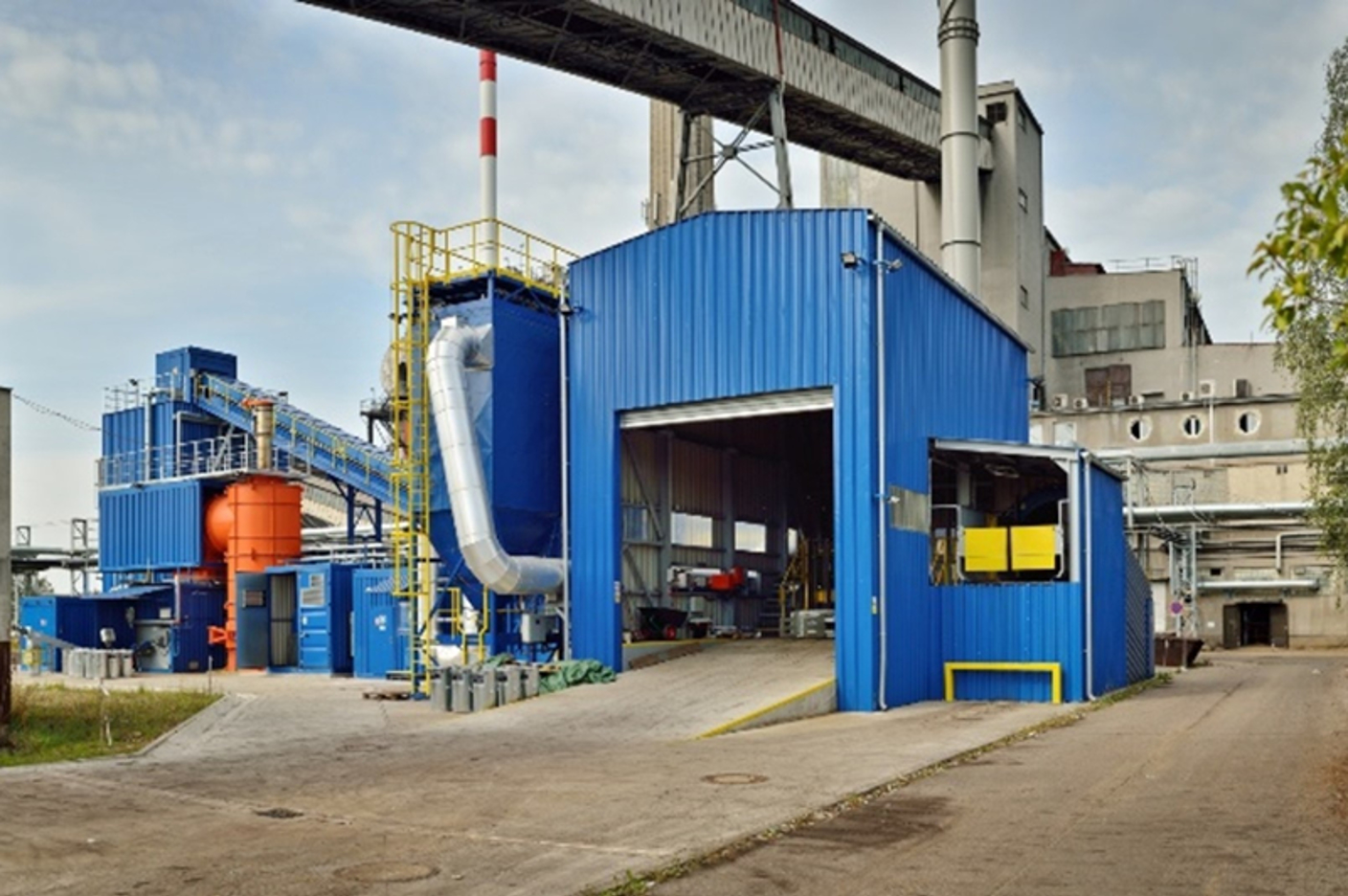
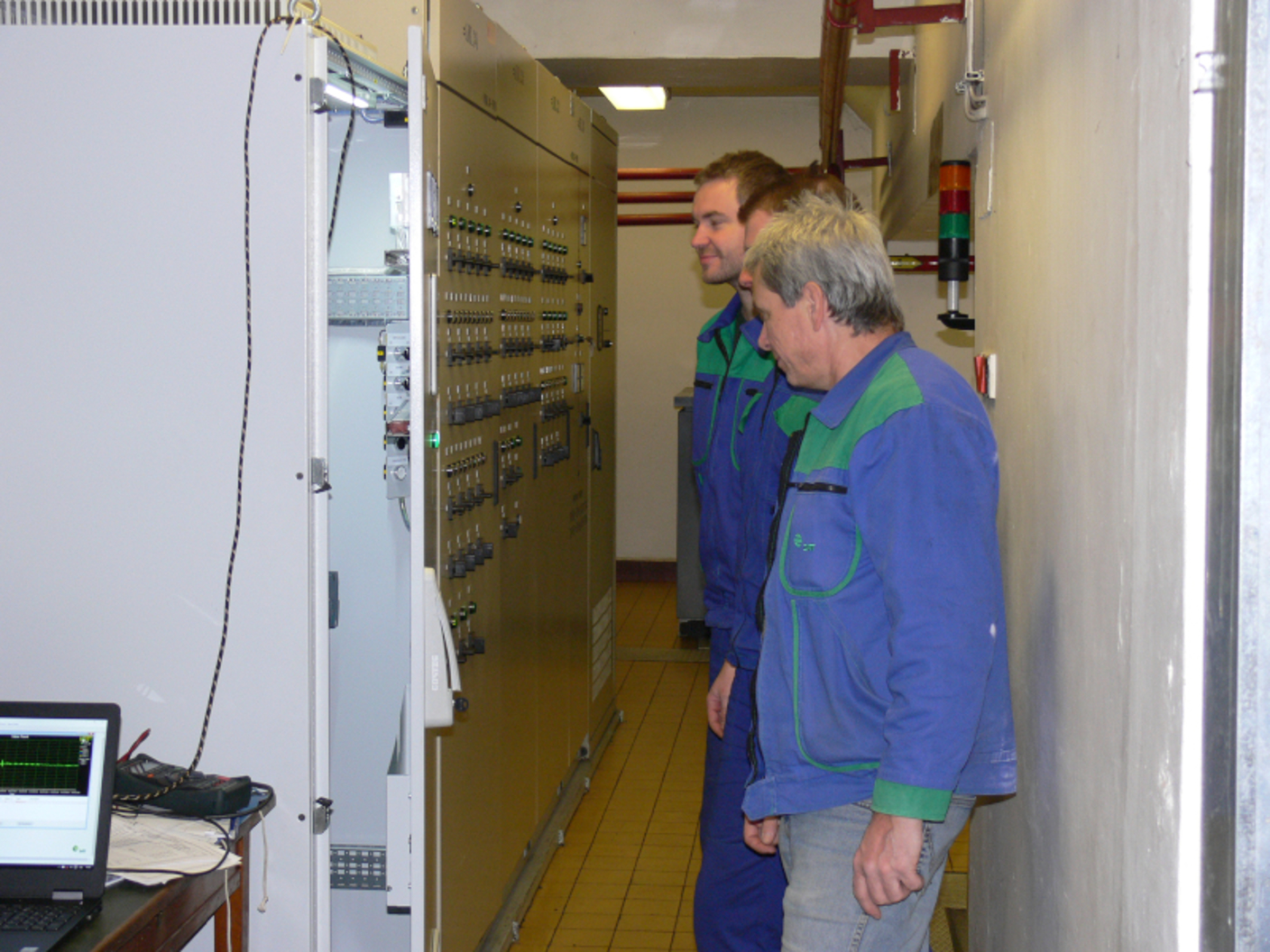
Service and maintenance
We design individual control systems mainly for our own projects, we also offer our know-why and know-how to other customers. In addition to controlling technologies on our own platforms, we also develop and manufacture special power blocks such as controlled rectifiers, converters, inverters, etc.
Advantages of our service
- Customer support and services in the field of project preparation
- Possibility of training customer employees
- Extending the life of the control system
- Customer care in the supply and repair of spare parts
- Warranty, post-warranty and guaranteed service
Product portfolio for thermal power engeneering
DCS (Distributed Control System) - To ensure high reliability and security of controlled large-scale technological operations, we design and supply a distributed control system on our own SandRA Synergy platform. DCS also includes HMI (visualization) at the level of engineering and operator stations. Functions such as data archiving, simulation, etc. are a matter of course.
Our company has long-term experience with the management of power blocks at thermal power plants of various outputs. The ZAT control system is ready for data processing and control of individual operational files, including comfortable handling and visualization. We use the SandRA Synergy product on the Z200 platform for the control and diagnostics of power blocks.
We provide monitoring and visualization with the help of products from Czech and foreign manufacturers. Geovap (Reliance) and Moravské přístroje a.s. (ControlWeb) are the Czech manufacturers of software applications. Of the foreign manufacturers, these are mainly Aveva (InTouch) and Siemens (WinCC) applications. If necessary, we can implement a project with SW Cimplicity.
We provide complete delivery, including field instrumentation and cabling.
Turbine control system
Solutions from basic design to implementation at the customer, including warranty and post-warranty service
Turbine regulator
Compact and robust solution for speed control of all types
and steam turbine sizes
Turbine protection system
Redundancy design with triplex I / O interface (selection 2 of 3 for measuring and controlling actuators)
Revolution synchronization
No impact connection of the rotary device to the turbine during shutdown of the unit
AVR Compact a AVR Power
We supply the automatic voltage regulator of synchronous generators as a solution for all types of excitation systems
DSD synchronization device
Compact repeatable solution designed mainly for ringless excitations or excitations of the smallest generators
Automatic secondary voltage regulation
Maintaining the required voltage and balancing the reactive power balance in individual network nodes
For substation control, we offer our own SandRA Z200 or Z210 control system or a control system compatible with the control of the entire block according to customer requirements.
We provide monitoring and visualization with the help of products from Czech and foreign manufacturers. Geovap (Reliance), Moravské přístroje a.s. (ControlWeb) are the Czech manufacturers of software applications. The foreign manufacturers are Aveva (InTouch) and Siemens (WinCC).
The diagnostic system is part of the SandRA Z200 process stations.
Combustion process operating files
- Transport and fuel treatment - internal coaling, mills and screens, burners
- Water management consisting of feed pumps, level control in the feed tank and regulation of the pressure / temperature of the steam outlet medium
- Air parts
- Flue gas tract
Boiler regulation circuits
- The level in the drum
- Boiler steam temperature
- Power (output pressure or amount of steam from the boiler)
- Boiler air pressure
- Vacuum in the combustion chamber
- O2 content in flue gas
- Screw feeder weighing
- DeNOX
DeSOx
Flue gas desulphurisation control, including control of all main and auxiliary equipment
DeNOx
Technology management to comply with NOx emission limits, eg using ammonia in technology
DeDust
Control of the ash separator technology used for flue gas treatment by dedusting method
DeHg
Solutions for controlling technologies to reduce mercury emissions not only in thermal power plants
Want to know more? Contact us!
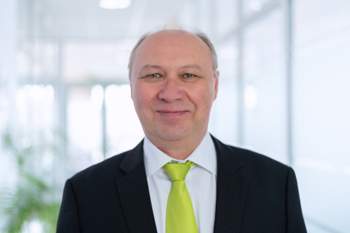